前回の製作で、以下の工程が完了しました。
・丸鋸本体の作製
・アルミプーリーによる変速機構の導入
・リニアシャフトのスライド機構の導入
・筐体作製
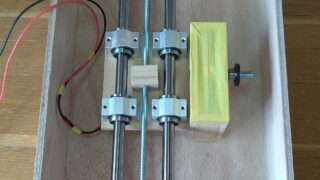
ですので今回は、「電動化」および「天板加工」
を行っていきたいと思います。
また、「目次01 電動化」を一読することで、
以下のことに関する知識が得られます。
・モーター駆動による鋸刃の自動昇降
・昇降を自動停止する方法(3路スイッチ / 4路スイッチ)
・鋸刃を昇降する方法(DCモーターコントローラー)
なお、本記事で行う工程は以下の通りです。
昇降機構 : 電動化
まずは、モーター駆動による昇降の電動化を行っていきます。
(※電動化は初めての試みであるため、改良の余地があるかもしれません。)
モーターの回転を伝動する方法はいくつかありそうですが、
今回は、「ポリウレタンベルト+プーリー」で行います。
[使用する材]
[動力系]
① DCモーター : 「12V, 400-500rpm」 1基
② アルミプーリー : 「外径16mm, 内径6mm / 8mm」 各1個
③ ポリウレタンベルト : 「径5mm」
[電気系]
④ 3路スイッチ : 2個
⑤ 4路スイッチ : 1個
⑥ スピードコントローラー : 1個
⑦ 電池ボックス : 「8本用」 1個
⑧ 単三乾電池 : 8本
⑨ 電線 : 「赤 1m / 黒 1m / 白 3m / 黄 2m 」
⑨’熱収縮チューブ :
[動力系の加工]
筐体の上面に穴をあけて、モーターを固定し、
端子に電線を半田付けして、収縮チューブで覆います(下画像赤枠)。
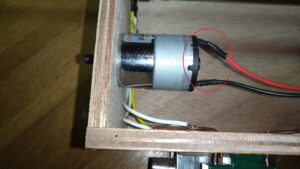
[電気系の加工]
今回は、配線を以下の4色に分類しました。
「配線の間違いを防ぐ」ことや「視認性の向上」を兼ねています。
赤、黒 : モーターに接続するもの
白 : 3路スイッチ、4路スイッチ間の配線
黄 : 電源に関連するもの
まずは、「3路スイッチ」の取り付けを行います。
※このスイッチは、昇降の自動停止を担います。
(4路スイッチとの併用で、外部操作による始動が可能となります。)
ちなみに、今回は以下のものを使用しました。
ボタンを押している間のみ経路変更が利く仕様です。
3路スイッチに電線を3本「L字型に」取り付けます(下画像赤丸部分)。
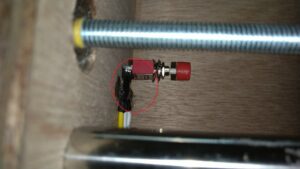
端(C): コントローラーへ接続 [黄線]
中央、端(NO、NC): 4路スイッチへ接続 [白線]

そして、丸鋸本体が「最上端、最下端」で押せる位置に、
3路スイッチを接着剤で固定します(下画像)。
(※今回は、モーターの側壁に触れて停止する仕様にしました。)
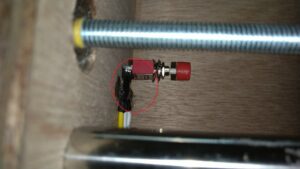
次に、筐体に4路スイッチ用の穴をあけます(下画像)。
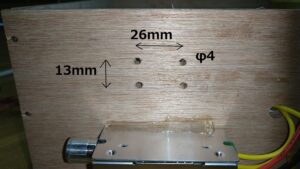
4路スイッチに銅線を4本差し込み、筐体に取り付け、
3路スイッチの白線に半田付けします(下画像)。
[※4路スイッチを介して、黒矢印の方向(3路スイッチ側)に電気が流れていきます。]
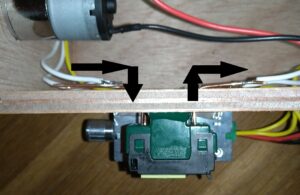
※4路スイッチも、経路の切替を行います。
(この切替によって、「筐体外での昇降操作」が可能です。)
ちなみに、今回は以下のものを使用しました。
銅線「1.6mm / 2mm」を差し込んで使用します。
(※4路スイッチでも内部機構が異なるものがあります。)
その後、「4路スイッチ / コントローラー」を筐体に接着します(下画像)。
また、配線用の穴(φ9)をあけます(赤枠部分)。

コントローラーは、「昇降速度 / 移動方向」の制御を担っています。
(材の厚み・硬さに応じて調整していきます。)
※昇降するためには、「正回転・逆回転」の動きが必要ですので、
逆転仕様があるものを採用します。
ちなみに、今回は以下のものを使用しました。
これには以下の機能が組み込まれています。
・逆転機能のトグルスイッチ ⇒ 「昇降 / 下降」の切替に必要
・速度調整のつまみ ⇒ 材の「厚み / 硬度」に対応可能
・通電時の赤色点灯
回路を自作する手間・知識が不要なため、オススメです。
仕上げに、電線をコントローラーに取り付けます(下画像)。
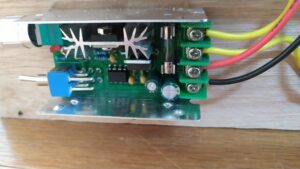
[コントローラーには以下のように接続します]
Power(電源) : 3路スイッチの黄線(+) / 電池ボックスの黒線(-)
Motor(モーター) : モーターの赤線(+) / モーターの黒線(+)
最後に、電池ボックスを筐体に取り付け、
単三乾電池を8本装着したら完了です(下画像)。

天板加工 : 取り付け
まずは、天板の取付を行っていきます。
[使用する材]
⑩ ベニヤ9mm : 「450mm × 600mm」 1枚
⑪ 蝶番 : 3個
まずは、天板として材⑩と筐体を蝶番で連結します(下画像)。
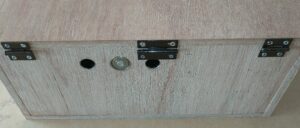
次に、丸鋸を駆動した状態で天板を下ろし、
天板に切り込みを入れていきます。
※鋸刃を左右に少しずらし、切り込みを複数回行い、
鋸刃-天板との間の擦れを無くすことで、静粛性が向上します。
天板加工 : アルミフレーム取付
次に、材を載せるためのフレームを取り付けていきます。
[使用する材]
⑫ アルミフレーム2040 : 「200mm, 400mm」 各1本
⑬ 六角キャップねじ : 「2020用, M4」 4本
⑭ tナット : 「2020用, M4」 4個
切り込み線を基にして、穴あけ位置を決定します(下画像赤丸・青丸)。
(※赤丸φ6 : ネジと鋸刃が干渉しないように座繰り加工を行います。)
(※青丸φ9 : 筐体外にあるため貫通穴で十分です。)

アルミフレームの角度調整には、φ9の穴に取り付けた「ねじM4」で行います。
(※敢えて大きな穴をあけることで、角度調整の余地を残しておきます。)
そして、アルミフレームを左右に取り付け、(下画像)
スコヤを用いて直角に調整します。

追加工
ここからは、「ストッパーとクランプ」の導入を行っていきます。
[使用する材]
[ストッパー]
⑮ MDF9mm : 40mm × 30mm 2枚
[クランプ]
⑯ L字型アングル : 2個
⑰ ボルト : M6, 60mm程度 2本
ストッパーは「縦40mm, 横30mm」程度に切り取り、
下から10mmの位置にφ6の穴をあけたら完成です(下画像)。
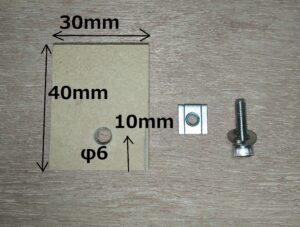
クランプは、市販のL字型のアングル(鉄製の厚みがあるもの)に、
「φ5の穴あけ ⇒ M6タップ立て」を行い作製しました(下画像)。
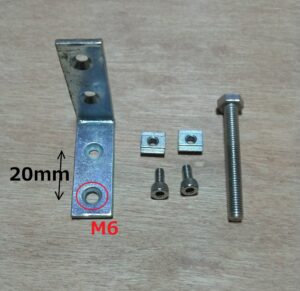
アングルはホームセンターで購入したものですが、
穴位置とフレーム溝との相性が良く、直ぐに使用することができました。
性能試験
ここからは、実際に使用して、測定した結果を以下に記しています。
(切断試験にはMDF9mmを使用しました。)
[結果]
(空転状態)
18V(rpm) : [80dB, 0m / 72dB, 1m]
21V(rpm) : [85dB, 0m / 74dB, 1m]
24V(rpm) : [87dB, 0m / 75dB, 1m]
切削高さ : 33.5mm
切削長さ : 370mm
締め
本製作では、減速機構を導入しました。
これによって、以下の利点が得られました。
・振動の抑制
・切削高さの増加
・高出力 / 低回転での使用が可能
しかし、以下の点に関して課題を感じたため、
改良を加えて納得できる作品に仕上げていきたいと思います。
・丸鋸本体の剛性の低さ(リニアブッシュ同士の間隔の狭さ)
・アルミフレーム取付穴の位置(角度調整がやりにくい)
・粉塵の筐体内部での飛散